veröffentlicht am 24.10.2024
Ob an der Uni, im Labor oder im Unternehmen: Wer für innovative Projekte eine bestimmte Laserkomponente benötigt, sucht häufig nach der Nadel im Heuhaufen. Oft besteht die einzige Möglichkeit darin, das entsprechende Bauteil speziell fertigen zu lassen. Doch auf wen ist Verlass? Wir haben hier fünf Kriterien zusammengestellt, die bei Auswahl eines Design- und Manufacturing-Partners helfen.
Vom Maschinenbau über die Mess- und Medizintechnik bis hin zu Bioanalytics: Alle diese Branchen benötigen maßgeschneiderte Lösungen aus den Bereichen Laser, Faseroptik, UV & UVC, die auf spezifischeAnforderungen zugeschnitten sind. Denn immer dann, wenn es um kritische Anwendungen geht, bringen Standardprodukte selten die nötige Präzision, Leistung oder Funktionalität. Dann sind Spezialhersteller gefragt, die exakt auf Kundenbedürfnisse eingehen können und neben Entwicklung und Design auch Prototyping und Fertigung aus einer Hand anbieten.
Doch was unterscheidet einen Spezialanbieter vom anderen? In diesem Blogartikel haben wir fünf Kriterien aus der Praxiserfahrung zusammengetragen, die maßgeblich zur Kundenzufriedenheit und zu langjährigen Produktlebenszyklen beitragen.
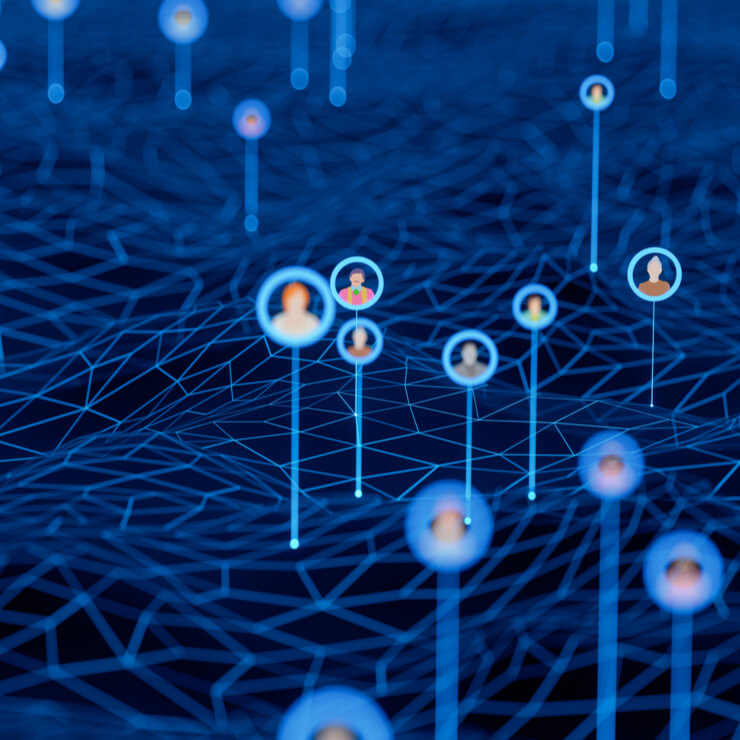
1. Einen Vertrieb suchen, der Ihre Sprache spricht
Erster Kontaktpunkt zwischen Ihnen und Ihrem potenziellen Auftragnehmer ist der Vertrieb: Hier werden bereits die entscheidenden Weichen für eine erfolgreiche und unkomplizierte Zusammenarbeit gestellt. Daher ist es wichtig, dass Ihr Ansprechpartner Ihnen aufmerksam zuhört, die richtigen Fragen stellt und Ihre Anforderungen präzise versteht. Idealerweise verfügt der Vertriebsmitarbeiter, mit dem Sie sprechen, über einen technischen Hintergrund und ein entsprechendes Verständnis für Ihre Anforderungen.
Stellen Sie darüber hinaus sicher, dass die Entwicklungsabteilung frühzeitig in Ihr Projekt eingebunden wird, um den Auftrag aus ihrem besonders geschulten Blickwinkel zu beurteilen. In dieser Phase werden alle Anforderungen und Bedürfnisse nochmals detailliert durchgegangen, hinterfragt und konkretisiert. Dies schafft Transparenz und weitestmögliche Planungssicherheit für beide Seiten. Besonders vorteilhaft ist ein solcher Prozess insbesondere auch dann, wenn Sie bereits ein fertiges Design haben, das produziert oder optimiert werden soll. So können Schwachstellen frühzeitig identifiziert und kostspielige Fehlversuche oder Umwege vermieden werden.
2. Fertigung von vornherein mitdenken
Ähnliche Vorteile bietet es, einen Partner zu wählen, der Ihr Photonics-Projekt nicht nur in der Design- und Prototyping-Phase unterstützt, sondern es bis zur Serienproduktion begleiten kann. Denn in solchen Unternehmen fließt das Know-how aus der Fertigung in die Entwicklungsabteilung zurück. Im Zuge einer umfassenden Betreuung wird diese daher von Anfang an die Umsetzungsmöglichkeiten durch existierende und neue Fertigungsverfahren im Auge behalten. Dies reduziert insbesondere an der Schnittstelle zwischen Prototyping und Serienproduktion potenzielle Schwierigkeiten. Durch stetige Iteration und engmaschige Zusammenarbeit können Synergien genutzt werden.
Falls sich nämlich erst zu einem späteren Zeitpunkt herausstellt, dass ein Bauteil aus fertigungstechnischen Gründen nicht wie geplant umgesetzt werden kann, müsste hier nachgebessert werden. Das führt nahezu unweigerlich zu Kompromissen, die sowohl die Qualität als auch die Lebensdauer Ihres Produktes beeinträchtigen können.
Legen Sie Entwicklung und Fertigung daher nach Möglichkeit in eine Hand. Dann erhalten Sie mit hoher Wahrscheinlichkeit Vorschläge für Laser- oder Optik-Designs, die auch tatsächlich realisierbar sind.
3. Weit in die Zukunft planen
Während Entwicklungszeiten im Consumer-Bereich oftmals kurz sind und die Produktion manchmal schon nach ein bis drei Jahren wieder heruntergefahren wird, basieren Spezialanwendungen in der Medizintechnik, Bioanalytik oder ähnlichen Einsatzbereichen oft auf ausgedehnten Vorlaufzeiten. Diese können rund 10 Jahre oder mehr umfassen, bis das Produkt in Serie geht. Damit sich eine solche Investition auszahlt, muss auch das Produkt anschließend entsprechend lange auf dem Markt bleiben. So fertigt IMM Photonics beispielweise schon seit fast 30 Jahren ein Produkt im Kundenauftrag und laut Plan soll es weitere zwei Jahrzehnte im Einsatz bleiben. Fällt Ihr Projekt in eine ähnliche Kategorie, so ist es wichtig, sich schon von Anfang an um einen Hersteller zu bemühen, der die entsprechende Beständigkeit über lange Zeiträume sicherstellen kann. Das sind in der Regel Unternehmen, die gut im Markt etabliert sind und über einen langjährigen Kundenstamm verfügen.
Je nach Markt müssen Teile aber nicht nur lange Zeit lieferbar bleiben, auch die Lebensdauer der Komponenten muss besonders hohen Ansprüchen genügen. Denn ob Auswahl der Bauteile, Art der Konstruktion oder die Sauberkeit in der Herstellung: All das wirkt sich auf die Langlebigkeit aus. Daher sollten Sie schon bei Auftragsanbahnung klarstellen, welche Anforderungen Sie an die Lifetime des zu fertigenden Produkts haben. Legen Sie außerdem dar, welchen Umweltanforderungen es im täglichen Einsatz gewachsen sein muss. Gegebenenfalls sollte der Hersteller in der Lage sein, Ihren Prototyp bestimmten Stress-, Rüttel- oder Klimazyklentests zu unterziehen.
4. Forschungen zur Schnelligkeit anstellen
Umgekehrt kann es aber auch sein, dass Sie schnell auf neue Technologien und Markttrends reagieren müssen. In diesem Fall sollten Sie Ihre Erwartungen in Bezug auf die Time-to-Market zeitnah adressieren. Wenn Sie mit verschiedenen Anbietern sprechen, dann lassen Sie sich anhand verschiedener Beispielprojekte darlegen, wie lange diese in der Regel von der Produktidee bis zur Markteinführung brauchen.
Welche Zeitspannen hier als schnell oder weniger schnell einzuschätzen sind, hängt selbstverständlich stark von der Komplexität des Produktes ab. So können erfahrene Hersteller wie etwa IMM Photonics einen einfachen Kollimator in etwa einer Woche designen. Nach Freigabe des Kunden geht dieser in Fertigung – und schon nach etwa vier Wochen halten Sie das erste, speziell für Sie entwickelte Produkt in Händen. Bei hochkomplexen, hochintegrierten Systemen kann sich der Zeitraum leicht über eineinhalb bis zwei Jahre erstrecken.
5. Reinheitsgebot beachten
Partikelverschmutzungen sind im Optik-Bereich eine große Herausforderung. So können beispielsweise bei Mess-Applikationen schon kleinste Teilchen in einem Modul die Qualität des Produkts und der Messung erheblich beeinträchtigen. Ein Risiko, das es zu vermeiden gilt – idealerweise durch einen Reinraum.
Hierbei gibt es zwei Optionen: Flowboxen, eine Art Mini-Reinraum, bieten bereits eine erhöhte Sauberkeit für Optiken. Ein deutlich weiterer Schritt in Sachen Sauberkeit und Qualität ist ein eigener, komplett abgeschlossener Reinraum, der für die Fertigung von optischen Komponenten klassifiziert ist. Eine eigene Luftströmungstechnik sorgt dafür, dass Partikel noch effektiver aus dem Arbeitsbereich entfernt werden.
Dadurch werden selbst kleinste Ablagerungen auf optischen Oberflächen verhindert. Der Zugang zu diesen Reinräumen erfolgt durch Personenschleusen, in denen spezielle Reinraumkleidung angelegt wird. Darüber hinaus gelten kontrollierte Umgebungsbedingungen. So werden beispielsweise Temperatur, Luftfeuchtigkeit und Luftdruck präzise reguliert, um optimale Bedingungen für das verbauen von optischen Komponentenzu schaffen. Unser Tipp: Sprechen Sie schon bei der Auftragsanbahnung die Frage der Sauberkeit an und forschen Sie nach, welche Maßnahmen hier getroffen werden.
Fazit
In der Regel werden Sie nicht über alle diese Kriterien auf den Webseiten potenzieller Partner hinreichend informiert. Vereinbaren Sie daher am besten ein erstes Beratungsgespräch mit den Herstellern, die für Sie in Frage kommen, und klären Sie Ihre Fragen persönlich.